Johannesburg, 10 Oct 2016
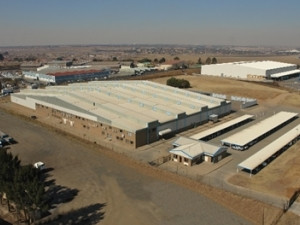
Adlam Engineering is a family-owned business and has been in operation since 1974. This means Adlam Engineering has more than 40 years of experience with the manufacturing of industrial machine components via turning, milling and gear-cutting.
Adlam Engineering is a rebuilder of mining equipment and designs. This has, over the years, enabled it to manufacture parts to the specification of OEMs. It is the first South African company to be accredited by Siemens as its repair centre.
Today, Adlam Engineering employs almost 300 people at its head office, in Boksburg, just outside Johannesburg, and has branches in Zimbabwe and Zambia. Its workshop premises of 12 000m2 houses 30 machines across five departments.
Adlam Engineering has contracts with mining houses, where it is contracted to attain high levels of on-time deliveries coupled with seven-day delivery lead times. This then means it has to keep component stock, and only assemble when orders arrive. It does sometimes keep stock of completed products. Late deliveries mean penalties.
Adlam's product mix is made up of standard products (for the mining sector) with pre-defined production steps and set prices; and non-standard products that are heavily reliant on the accuracy of costing and estimation.
This variety made it hard for Adlam to trace and plan properly, considering that a normal finished product could contain up to 200 components.
After having considered several APS systems, Adlam chose Preactor 400 APS. The choice was done by comparing the wide range of features and the ease of replacing the different flavours of Excel spreadsheets across all departments.
nCoded Solutions partnered with Adlam Engineering in the implementation of Preactor 400 APS, and the project started in January 2014. By May 2014, the planning department was able to use Preactor to schedule all the production resources considering the availability of raw materials and components.
The main objectives of the project were to:
* Improve visibility and traceability;
* Improve on-time delivery;
* Reduce planning time; and
* Assist estimation to quote accurately.
Thomas Adlam, Technical Director, said: "We are pleased to have partnered with nCoded Solutions for the implementation of Preactor, as they brought with them excellent supply chain planning knowledge. For us, it was important to work with people who have a deep understanding of how to merge in-house written systems and APS solutions."
Frikkie Bekker, Planning Manager, commented on the project: "It's amazing how easy the implementation of the project was. We started to use Preactor just the day after the software was installed, leaving behind our previous working methods. Before, the major amount of my time was spent adjusting the schedule due to delays in supplies or breakdown of machines, with little visibility. Now we can focus on real exceptions and anticipating problems in advance.
"In August 2014, our APS maturity had improved so much that we had integrated all our processes into Preactor and also implemented many KPIs guided by Preactor standard reporting tools. At this time, we were also using Preactor Job Card Reports, Routing Sheets Reports, etc - by this time, we couldn't live without Preactor. When the server goes down, we are blind."
nCoded Solutions approached the project by designing, in Preactor, a quoting module where all quotes are created and stored. This was followed by a design of an order capturing mechanism where real orders are created. Adlam Engineering calls this module Demand Management.
All orders sitting in the Demand Management module are downloaded into the APS Finite Schedule (another Preactor module) and are thereafter scheduled across 30 machines. The number of operations scheduled within the Preactor APS Finite module vary between 30 000 to 40 000. This translates to about 3 000 sales orders at a time. The scheduling process takes 30 minutes.
Real-time shop floor feedback is done against the schedule to keep it up to date, and KPIs such as plan versus actual, adherence to plan, plant utilisation and plant performance, etc, are monitored.
The project took six months.
Adlam Engineering asked nCoded Solutions to stay on after the project and assist it with other productivity improvement initiatives and programmes around Preactor.
This is what Adlam Engineering looks like now - two years later.
1. Traceability and visibility
a) Customers and suppliers are able to track progress and future demand via Adlam Engineering's Web site.
b) Sales personnel receive texts and/or e-mails when their selected orders are complete in production - in real-time.
c) Everyone at Adlam is able to see the progress (and location) of any order/job within production using the Adlam Engineering's MS Reporting Services portal (they refer to this as their Intranet).
2. Customer service
a) Customer service was improved by 20%.
3. Productivity improvement
a) Throughput was improved by 22%.
4. Converting Adlam Engineering into a smart factory
a) Automated planning with Preactor.
b) Shop floor tracking via touch screens and scanners.
c) Dashboards for real-time monitoring.
d) Collaboration between customers and suppliers via Adlam Internet.
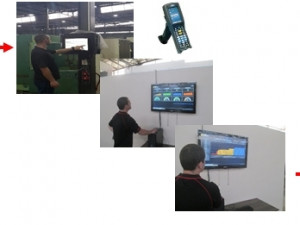
Share