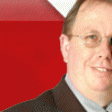
In yachting, the expression "sailing close to the wind" refers to the situation where the boat moves as efficiently as possible by heading in a direction that is close to the oncoming wind, but not too close. If the yacht steers closer to the wind, the sail collapses and the resulting instability severely retards or even reverses the yacht`s speed. Similarly, if the yacht takes a conservative course that is not "close enough to the wind", it is likely to be overtaken by race competitors who have learned to perfect their sailing.
This concept of operating at optimal operating conditions is not limited to yachting or the physical world, but is frequently found in business and in the realm of human behaviour. The proverbial "straw that breaks the camel`s back" similarly describes a set of stable circumstances rendered unstable by the addition of one just one more insignificant stress to the system.
As manufacturing companies increase efficiencies by operating closer and closer to the optimum, so their resilience to minor upsets is diminished. Because under these conditions multiple systems are frequently under strain and near breaking point, a single upset can trigger a chain reaction of failures, leading to sudden, even catastrophic system failure.
Maintenance managers will easily recognise this dilemma in their own field. We all know that short-term cost-cutting can be achieved by cutting back on preventative maintenance. We also intuitively understand that it is possible to over-maintain equipment, leading to inefficiencies and unnecessary cost burdens. One answer is to use scientific measurements and techniques to predict failure as accurately as possible, and then coincide maintenance just before failure, in other words "sail close to the wind". Whether or not this is implicitly understood, the maintenance manager is weighing up the risk of major failure against the opportunity cost of postponing maintenance on a particular piece of equipment in favour of production. This risk is a combination of the probability of failure and the consequences of the failure.
Understand implications
The same principles of managing risk to "sail close to the wind" are found in many aspects of manufacturing and business in general. The result is that business and production managers alike are easily able to understand the implications of investments that reduce inherent risk and which lead to intrinsically more stable and optimised operations.
Safety professionals need to understand how the overall organisation acts as a system with many interrelated elements.
Gavin Halse, MD of ApplyIT
Why then are safety practitioners so bad at building a solid business case for safety investments? Perhaps put another way, why are safety professionals rarely entrusted with significant budgets? Perhaps the answer lies in the metrics of choice of safety professionals - namely incident rates.
A recent interesting study by the Centre of Safety Research at Leiden University showed that between 1997 and 2004 (for which data was available), there was no correlation at all between the various incident rates (lost time, serious and fatality rates) and the profits of companies in the oil and gas sector. The study made an unforgiving conclusion: profits were unrelated to any safety parameter.
The same finding is probably true for other established heavy manufacturing industries. Does this mean that any business case based on these established safety metrics is fundamentally flawed?
The Leiden study went on to show that implementation of various safety management systems around the world has succeeded in systematically and progressively reducing the incident frequencies. This means that many safety management systems are good at what they purport to do, but does not help the business case unless these incident frequency reductions can be expressed in financial terms. If profit is unrelated to the number of incidents, then any financial metrics that attempt to show otherwise are likely to be treated with some scepticism.
The answer to building a credible business case lies perhaps with another finding in the same study. The researchers at Leiden went on to find that since 1970, while minor incidents were decreasing, a systematic increase in major disasters and fatalities had occurred, as reflected in re-insurance industry statistics. So while incidents were on the decline, serious disasters and fatalities were increasing.
Sound business case
Importantly, there was no measured correlation between minor safety incident rates and serious disasters. Business managers will know that depending on the severity of a disaster, profits can indeed be severely affected. Production downtime, supply chain disruptions, contractual penalties and direct costs of restoration are real financial parameters that can be quantified, and strike fear in the hearts of business managers; far more so than a slight increase in the lost time incident rate.
A sound business case for any investment that reduces risk needs to take account of many factors, and demonstrate how the particular investment will interact with other aspects of the business in reducing overall risk.
The reality is that in a competitive environment, companies do indeed sail close to the wind. They balance risk against reward - and profit is the strongest measure of reward. However, this sailing close to the wind is typically not the exclusive preserve of safety professionals and their metrics - it manifests in all elements of production, including engineering, operations, maintenance, human resource management and cash management: in short, every aspect of business. The frequently chosen "close-to-the-wind" optimum places the company at greater risk of a disaster or severe incident with fatalities, which will be recognised by astute managers who will be willing to invest to mitigate the risk. However, the leading indicators of impending disaster are not found in the traditional safety incident statistics and this is perhaps why some safety investments don`t get approved.
Safety professionals need to understand how the overall organisation acts as a system with many interrelated elements, many which are simultaneously under strain, and which results in a certain risk profile. There is indeed a role for traditional safety metrics in building a business case for investment, but the emphasis should be on a more holistic view and the interrelationships between the new system and other elements of manufacturing, to reduce the overall risk of disaster.
Share