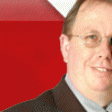
In a manufacturing business, it is typically the production manager who is responsible for operating the facilities in a safe and responsible manner. In addition to production targets, a production manager's key performance areas frequently include process safety and the implementation of systems to ensure that safety standards are maintained.
Most production managers will be familiar with the concept of a risk assessment. Risk assessments, whether in the design, commissioning or operations stage of a plant's lifecycle help to identify risks that have the highest probability of occurring, and simultaneously have the highest impact in the event of an incident. Once these priority risks are identified, compensating measures can be implemented.
In all safety legislation such as the Occupational Health and Safety Act, risks need to be identified, and as far as possible eliminated before resorting to compensating measures such as personnel protective equipment. However, complete elimination of risks is generally impractical, and where risks cannot be totally eliminated, potential hazards remain.
It needs to be recognised that all plants go through stages in their lifecycle, from the initial engineering and design stage, through commissioning, into routine operations and thereafter modification and eventual retirement or decommissioning. A number of other changes are taking place simultaneously as the plant matures; minor plant modifications, changed operating protocols and procedures, evolution of process technology and better production efficiencies. Each of the stages in a plant lifecycle are characterised by a predominance of and accessibility to specialised skills; for example engineers are heavily involved during design and commissioning stages, but less so during routine operations.
Identifying potential hazards
When plants are designed, the process engineers spend a significant amount of design time identifying potential hazards in the operating plant. The most widely used design technique at this stage is the hazard and operability study (Hazop). In the Hazop, a formal process is followed to identify hazards and rate these according to the probability of occurring and the consequences of failure. This is the first real risk assessment relating to that particular plant or process.
It needs to be recognised that all plants go through stages in their lifecycle.
Gavin Halse, MD of ApplyIT
These Hazops are generally performed at a stage in the design process when fundamental safety design standards have been set and are well understood by all. For example, the use of hard-wired trips, plus mechanical protection (example relief valves) and software lockouts all introduce some level of protection and may (for example) be compulsory for all pressure vessels in the plant. During the design phase, these safety standards are relatively easily enforced, and because they form the underlying basis of the design, the result is usually a plant with a high integrity safety system.
However, after a number of years and as plants move through their lifecycle, it is frequently the case that the original design standards are changed, during which time many process modifications have been made. This situation is also sometimes worsened by the reality of the business being passed between a number of shareholders; each of whom impose a new sets of engineering standards on the hapless production manager.
During plant modifications, unless each change complies with the overall safety protection philosophy of the rest of the plant, operational safety may be severely compromised. Operators cannot realistically be expected to remember and operate with multiple design standards - yet this is frequently the reality in older plants.
To address these problems, production managers can implement formal systems for process safety management. These management systems represent best practice in an industry and provide a solid framework for ensuring that the original design and operations standards are maintained during a plant lifecycle.
There is at the same time also an excellent opportunity to raise the bar and introduce computerised systems in support of the process safety management systems. There is a strong case for having all relevant information in a single database. This computer system can be configured to cater for both the design and operations phase of the plant lifecycle. An effective computerised system must rigorously enforce procedures for the right way to do plant modifications, build in the safety aspects, and make this information accessible in a common database that is used by day to day plant maintenance, safety and engineering users. In this way the original Hazop information is not lost, but becomes part of active controls during plant modifications and operations.
As changes take place, the Hazop is correctly updated and rules for issuing permits to work are updated within the same system.
A comprehensive computerised system will retain relevant safety related information from all phases of the plant lifecycle and be tightly integrated into day-to-day operations. For example, the initial risk assessments in the design stages should be carried through into all plant modifications and into actual operations (for example, maintenance work order and issue of permit to work).
Introducing such a computerised system can act as a catalyst to introduce and enforce a best-practice culture in the company. In combination with the right skills and an enabling culture in the business, this integrated and holistic approach can be the solution to a production manager's need to deliver effectively on his job.
Share