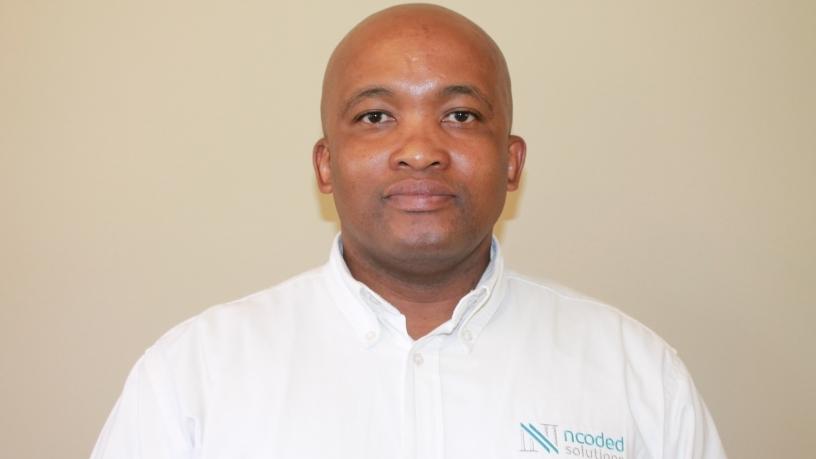
In manufacturing, there are two classes of companies: those that rely on an advanced planning system (APS) and those that don't. It's a crucial differentiator, and astute companies would adopt such a system in the blink of an eye. Yet, while utilising an APS is competitively crucial, it doesn't happen overnight.
"I'd say there are three customer groups we deal with," says Lance Zikalala, Managing Director at nCoded Solutions. "The customers who approach us the most often are those with an APS that needs to be configured. Then there are the manufacturing companies who don't yet realise the purpose of an APS, believing planning can be done manually - that scheduling is so simple all you need is a spreadsheet. In between them, the companies who realise that purpose, but are price sensitive or don't know how to proceed with adopting the solution. They might hear about it in industry circles, but still can't really figure out what works for them."
Many ways to manufacture
Manufacturing is a catch-all for an array of different techniques and processes. Common distinctions include discrete and process manufacturing, both categories for a deep bucket of different processes and variables dependent on the company and its sector.
Discrete, in Zikalala's words, is, for example, manufacturing a watch. There are many parts to a watch that have to be made independently, as components, and then assembled. Those components, such as the straps, casing, dial, etc, may change depending on the product order. Someone could order a watch with a black leather strap, while another one could order a watch that has a white cotton strap. In short, a machine on a discrete line might not necessarily create the same product with the same quantity all the time. Balancing, prioritising and sequencing those orders is fraught with complexity.
Process manufacturing focuses on just one item, such as paper. It continually produces the same product over and over again. While less complex than a discrete system, process tends to use larger, more expensive machinery that need to run continually in order to capitalise on their investment. These can blend. For example, a car manufacturer represents a discrete line, yet the individual machines in that line may be process orientated. A machine that makes car handles will do only that, but it contributes to a wide variety of vehicles. This is called repetitive manufacturing.
But even such categories don't quite illustrate the many variables and processes that different manufacturers can develop. There are at least eight factors that can influence a manufacturing strategy, including demand variability, the number of vendors and different types of shop floor planning.
Hence the need for a system that is tailored to managing those processes while still being deployable and scalable in turnkey capacities.
Why advanced planning matters
The APS's role is to ensure those processes are executed smoothly. For example, changing the colour on the watch strap means washing and prepping the line. This may seem simple, but even the task of switching from white to black paint, as opposed to switching from black to white paint, is different (in this case, the black paint line would have to be more thoroughly washed due to the colour intensity - in industry parlance, this is called dark-to-light sequencing). As for the paper machine, a matter of trimming reams to different measurements can heavily increase changeover costs. Even a routine event such as scheduled maintenance can throw a spanner into the planning process.
Those little nuances matter if a manufacturing line is to be efficient and effective, hence the APS. This was a task once left to humans, and there is still a prevailing view that people can do the job just fine. But a recent project at an nCoded customer, a cable manufacturer, shows things differently, says Zikalala: "They moved to an APS because their planner was retiring, and he had all this knowledge in his head and many Excel spreadsheets. We needed to formalise, to trap his knowledge onto a system. You can't do this type of planning from your head anymore, or from a spreadsheet. The mature companies know this. As soon as the customer started using this APS tool, they started seeing other benefits. The cost saving in that business overtook the earlier objective they had of having a system that would take in the knowledge."
Mature approach to modern planning
A key phrase there is the maturity of the company. As illustrated earlier with the spectrum, APS as a solution isn't quite understood, let alone valued, at first. Companies confuse it with ERP functionality, often because ERP vendors might argue they can add APS-style services onto the ERP. But this is not functional: ERP, being financially strong, is focused on historical data. It can handle the orders and help plan the specifics of each. Yet it cannot look forward.
An APS is financially weak, but forward-looking and specialises around planning and scheduling efficiency. If the ERP is a GP giving a general overview of what had happened, and could happen, in a perfect environment, the APS is a surgeon, ready to hone in on specific areas while predicting the future of what is likely going to happen given the current constraints. In the case of manufacturing, the APS ensures all the various processes of a manufacturing line are ready to deliver in tandem to orders processed by the ERP.
Thus the first step of maturity is to recognise the difference between an ERP and APS. They complement each other, but are still very different systems. Then it's the process of working out what the APS can do and how it can be done. This last part catches many companies off-guard. They often buy an APS, but don't realise how crucial the specifics of the configuration are. To get to that stage, they must investigate the planning practices of their sectors, as well as the process blends on their manufacturing floor.
"It's important to understand what is best practice in that manufacturing type industry," says Zikalala. "What methodology works in that industry? What's the domain expertise? If I move into a discreet environment, this is what works. So, as the solution, I am touching issues that are relevant to them. Simply bringing in an APS offers a mixed bag of things if it is not configured correctly. For example, in the process industry, there is no one size fits all.
"A paper company can face issues of deckling/trimming optimisation; a chemical company can face issues of packing and tanks optimisation; a foundry's heat and floor space maximisation - electrical wires, steel companies - all these are process companies. They have the same class (process industry), but with different dynamics such as forecasting and variability in capital investments."
The introduction of an APS is nuanced, yet incredibly potent. If configured to the requirements of the company and its industry, an APS dramatically reduces uncertainty and has been proven to create double-digit percentage gains on delivery performance, plant productivity, and labour overhead - and a reduction in raw material use. It is a major boon for strategy and hugely empowering for the parts of the business that aren't as focused on financial systems.
But to get there, companies must go through three stages: realise that an ERP and APS are complementary yet fundamentally different; interrogate their needs in order to select the right APS software tool; and finally, have the APS configured appropriately for their desired outcomes.
Share