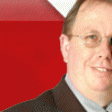
The velocity of change in manufacturing businesses is unlikely to slow, requiring the CIO of a manufacturing company constantly to acquire and develop new skills. These range from refreshing your technical knowledge, developing people skills and maintaining strategic insight of the industry in which you operate.
When faced with complex, seemingly insurmountable problems it is always helpful to rise above the detail and view the strategic landscape from high. By understanding the longer-term patterns and trends, it becomes far easier to put day-to-day IT decision-making into context.
Developing IT strategy in manufacturing requires a balanced and holistic approach. It is unnecessary and unwise to follow hype cycles blindly and at the expense of your stakeholders. It is necessary for process companies occasionally to adapt new technologies to extract a competitive position, and I am not suggesting that innovation and early adoption of technology does not have its place.
Developing IT strategy in manufacturing requires a balanced and holistic approach.
Gavin Halse, MD, ApplyIT
However, those who rode the Y2K/ERP upgrade, e-business, and more recently CRM bandwagons may now be feeling that perhaps it would have been better to hold back a little, because true competitive advantage probably lies elsewhere in the industry. Certainly, by spending less on annual hype issues, you may have been able to develop the foundations for better business in other, more relevant areas.
What then are the IT-related characteristics of a manufacturing company, which all need to be addressed in a balanced approach?
Commoditisation
Manufacturing companies operate in a world of ongoing consolidation resulting from the trends of globalisation and commoditisation of products.
The improvement in global logistics and relaxation of trade barriers allow companies to locate new production plants at the point where raw material and other input costs are optimised against logistics costs.
Existing plants, unfortunately, are much stuck where they are and need to compete in an environment where there may be some competitive disadvantages. The result is that fixed costs are cut back as far as possible. For IT professionals, fixed cost cutbacks usually translate to IT budgets being slashed, or at best not increasing year on year. In businesses where IT lacks the credibility to argue otherwise, cost cutbacks can cut deep into the fibre of the business itself, leaving it vulnerable.
Asset- and technology-intensive
Manufacturing companies are asset- and technology-intensive. Building a chemicals plant on a competitive scale requires enormous capital investment and takes years from product conception to first commercial production.
Profitability is even further away, frequently taking five years to a decade to achieve. In the world of IT, however, five to 10 years can represent two or three successive generations of completely new technologies. So it is important to understand that the time scales involved are fundamentally mismatched.
Short-term, hype-driven initiatives are sure to be tactical and therefore unlikely to be in line with the longer-term business strategy. IT systems that support the process of design, construction, commissioning, operation and maintenance of a chemical plant need to be architecturally sound to survive generations of IT solutions that will come and go over the plant lifetime. Technology management and management of key operating knowledge remain important as the initial design and commissioning team move to new projects.
Complex supply chains
Manufacturing companies, particularly process companies, operate within complex supply chains with additional constraints and fewer degrees of freedom than, for example, discrete manufacturers. This is due to the nature of raw material availability, product demand patterns, moving bottlenecks, shelf life issues, unplanned shutdowns or significant plant failures requiring complex startup procedures. Process supply chains involve fewer SKUs but have higher variability within SKUs and the manufacturing process itself. Supply chain solutions for manufacturing companies can therefore be highly specialised and industry-specific.
Manufacturing execution systems (MES)
Manufacturing companies are characterised by having an MES layer, including process control integration, management information and laboratory management systems. There is no doubt that MES and traditional IT are rapidly converging. This set of applications and systems introduce issues of governance, integration and specialised expertise and have a direct bearing on IT investment and value opportunities for a manufacturing company.
Safety, health and environment (SHE)
Manufacturing and process companies are characterised by a higher emphasis on environmental, health and safety issues than many industries. This is coupled with the various improvement or quality management processes that need to be supported. Effective management of SHE remains a critical aspect of such businesses, because a single incident can have severe consequences for stakeholders and ultimately the business itself. Sadly, many IT systems do not adequately support companies` operational SHE requirements.
A balanced approach to the application of IT in the manufacturing industry is required. By understanding the characteristics of the industry and the capabilities of IT solutions, IT can be a substantial enabler of business competitive advantage.
Share