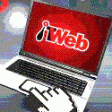
The University of Johannesburg (UJ) is exploring the use of 3D printing, also known as additive manufacturing, to address SA’s social housing backlog.
Vice-chancellor and principal professor Tshilidzi Marwala took to his Twitter page this week to showcase a model of a six-room RDP house, revealing it was built in a day using 3D printing.
It forms part of the UJ’s Faculty of Civil Engineering and the Built Environment partnership with the Department of Science and Innovation (DSI) to pilot and demonstrate 3D printing for sustainable human settlements development in SA.
Marwala comments that the university’s 3D printer is fast, saying: “If we invest in this technology…we can provide our people with decent housing fast and end informality.”
Responding to a question about whether the 3D-printed house is strong, Marwala says “very strong”.
3D printing is a technique that uses a device to create physical objects from digital models. The range of 3D-printable materials has grown significantly over the years, making the technology appealing to a wider array of industries.
In SA, the DSI, together with its entities, has led a number of 3D printing initiatives and proofs of concept, in response to some of the local challenges like the public housing backlog.
Even though the RDP housing programme has been in existence for a number of years now, fraud and corruption have often been identified among the barriers that hinder delivery of the country’s social housing programme. This has resulted in qualifying citizens not being able to access adequate housing.
In this case, the use of 3D printing is considered to provide a cost-saving and fast method of constructing the subsidised houses.
In addition, South Africa wouldn’t be the first country to build 3D-printed houses.
3DCP Group, a Danish 3D printing start-up, unveiled its first 3D-printed concrete tiny house in Europe, according to a report.
Located in Holstebro, Denmark, the building is said to be designed as an affordable option, housing all necessary amenities in 37 square metres. The overall aim is to build better, faster, greener, and to reduce the amount of strenuous work in the construction process.
Share