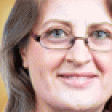
Early in 2008, William Weber needed power immediately for an extension to the 14th Avenue MTN campus in Johannesburg. Weber is core implementation manager for the mobile operator. He soon discovered he was heading into blackout territory, however.
Additional grid electricity was not going to be available after all. Despite previous assurances from the city's electricity provider that it was building more capacity in the Fairland area, 14th Avenue was connected to an overloaded substation. The provider reckoned it would take two years to supply the additional power.
To Weber, his options were simple. Lose a lot of business for MTN, or organise alternative power to the tune of 3MW if at all possible. And he had only a month or two to evaluate his options.
Calculations soon showed that even if MTN had a farm somewhere in the Karoo with enough space for enough solar panels, solar was not going to happen. The reticulation (electrical infrastructure) to bring in any form of alternative energy from outside the campus was simply not in place.
A separate experiment
Meanwhile, Weber had worked with electrical engineer Hans Auret, from Claassen Auret Incorporated (CAI), to supply base stations across Africa with alternative energy. Auret is semi-retired and enjoys designing things between long road trips.
In the first quarter of 2008, the two were looking at powering a test switch (a type of data centre) on the campus extension with something novel: an experimental baseload gas power plant.
'Baseload' means consistent power generation 24/7. A gas-powered baseload plant would boast about half the carbon footprint of coal-generated electricity.
Conveniently, the nearest Egoli Gas pipe was only 2.3km down 14th Avenue. In early 2008, rolling blackouts had not really started yet, so few industries focused on gas as an alternative. The gas provider was open to price negotiation.
Weber and Auret were well on their way to ordering an expensive, sophisticated Jenbacher gas engine from Austria for their 1MW power experiment.
Then an MTN board meeting halfway through the first quarter of 2008 - halfway through the planning of the experimental gas power plant - changed Weber and Auret's ideas at a stroke.
A bigger gamble
It was bad enough that Weber did not have additional power for the campus extension. Worse, the board had to grapple with its South African billing data centre in Newlands running at capacity. The billing would need to move to the planned new data centre at the 14th Avenue extension. But this would require even more power.
So the board decided to kick the experimental baseload gas plant up a few notches. It was now going to be twice the size, 2MW, and power both the new billing data centre and the test switch on the campus extension.
We promised the board a return on investment in about four years.
Willem Weber, MTN
It would still be a gas tri-generation plant, as Weber and Auret had planned. With tri-gen, specialised engines burn gas, generating both electricity and heat, as well as heat converted to cooling, which can then be fed to data centres and other buildings on a campus.
The design they wanted to use could only be scaled up to 2MW, though, because that was how much gas they could buy at the time.
Sleepless nights and many new grey hairs followed. By the end of the first quarter of 2008, Weber and Auret had scaled up their original 1MW plan to 2MW.
They ordered another 1MW tri-generation gas engine from GE Jenbacher.
Now they had to make technology that was unheard of in commercial power generation in Africa work well enough for a mission-critical data centre.
Grid power availability had evaporated at a bad time. The same was not going to happen with the gas power plant.
"When we do a calculation, we design for the worst efficiencies on the machines, the worst output from the absorption chillers to convert heat into cooling," says Weber.
"Because tri-gen was new to us, we were extremely conservative. When we first presented to the MTN board, they were sceptical about the UNFCC (United Nations Framework Convention on Climate Change) carbon credit application, so we excluded that in the original business case. Later on, MTN made a statement at board level that we could apply. We promised the board a return on investment in about four years."
Such a speedy return rides on a number of critical factors. In fact, 10 massive spreadsheets' worth of operational cost model, tweaked and tweaked again by Auret and his team.
The existing centralised MTN campus infrastructure for electricity, heating and cooling made a great fit for tri-generation.
Weber and Auret scrutinised carbon credits, actual cost of buying electricity or gas, plus price escalations over 10 years, and the energy the whole campus would use for chilled water and heating per year, as well as expected carbon taxes.
Crucial were the gas engines' efficiency and converting every bit of heat into cooling: a double absorption chiller process was required to make the numbers work well.
In addition, the gas supply must be steady, both in pressure and energy content, so that the entire conversion process runs predictably and efficiently.
A big plus for the data centre is that the Egoli gas distribution network is itself powered by gas, effectively making that gas an energy source independent of grid electricity.
Concept to completion
For the data centre and the test switch, the primary source of power is the tri-gen plant, with diesel generators as backup, and City Power's Eskom power as the third option.
With Auret's conceptual design for the tri-gen complete, consulting engineers Chris Leeson from CAI and Pieter de Bod from RPP took over on the detailed designs and construction of electrical and mechanical aspects of the tri-gen plant.
Architects specialising in data centres, Lizamari`e du Plessis and Maryke Cronje from ProjectWorks, sequenced and co-ordinated services for the intricate project plan's processes, consultants and contractors. Engineering project managers ISF Services worked with contractors and sub-contractors, implementing and enforcing day-to-day project programming.
Construction on the tri-gen plant started in October 2008.
Getting a brand-new idea from concept to commissioning is not for everyone. Keeping a sharp eye over everyone and everything was veteran Auret, steering the project through uncharted territory.
When we take the increased efficiencies of the machines and the UNFCC carbon credits into account, we've got just over two years' ROI.
Willem Weber, MTN
In July 2010, Jenbacher commissioned the first gas engine, and the second one two months later. That August, MTN invited the press to the completed tri-gen plant at 14th Avenue.
By this February, Weber could quote rudely healthy numbers for the plant.
"When we take the increased efficiencies of the machines and the UNFCC carbon credits into account, we've got just over two years' return on investment," says Weber.
In March this year, MTN commissioned another tri-gen plant in Centurion, at 4MW, double the size of the one at 14th Avenue. This plant will eventually power a data centre planned to be bigger than 2 000 square metres in its later phases.
"The Centurion plant is lower in capital, and has a lower operating cost than 14th Avenue," says Weber.
However, negotiating the gas contract price was much tougher this time around with Sasol. At first, Weber was told they were way down a waiting list for gas.
"Without the right price on the gas," says Weber, "it would not have made sense."
Making history
Weber, Auret and their team of over 70 people got MTN's South African billing data centre and a test switch going at 14th Avenue in time, on the first commercial tri-generation power plant in Africa.
Currently, the two engines can supply about 30% of the electrical power needed by the entire campus during summer when more cooling is needed, and about 40% of the total campus demand in winter, says Auret.
Per hour, he says, the two engines consume about 4 800kW of gas energy, and produce about 2 000kW of electricity. In that hour, the tri-gen plant recovers 2 400kW of heat, which is converted into 1 600kW of cooling.
Should additional gas supply become available, MTN will increase the 2MW Fairland plant six-fold to 12MW to move the campus towards power-independence, MTN SA CEO Karel Pienaar was reported saying in August 2010.
For MTN, powering data centres with tri-generation plants pays off quickly.
First published in the August 2012 issue of ITWeb Brainstorm magazine.
* Article first published on brainstorm.itweb.co.za
Share