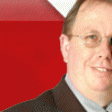
Supply chain projects often fail. And despite extensive documentation regarding the factors leading to failure, the number of companies that are still unable to accurately plan and execute production to meet demand remains surprisingly high. These companies, which are sometimes characterised by near-chaotic production environments, often seem to hold the belief that there are too many unknowns in their supply chain and that somehow this makes their business "unique" or "special".
It is interesting that some of these companies have been running relatively stable production processes for many decades, yet they still seem incapable of preparing a simple production plan based on demand.
On closer inspection, some of these companies are running state-of-the-art ERP systems, fully capable of detailed and highly optimised production plans. Yet production managers continue to ignore the system-generated plans and produce what is expedient and what appears to meet the short-term optimum.
The result, of course, is that the ERP system continues to produce plans that are out of synch with production, which further reinforces the perception that the plans are there to be ignored. This cycle can become entrenched over many years and it often takes an outside perspective to point out just how bad the situation has become.
Mathematicians will be familiar with the concept of stability when describing a model. Complex models can become unstable by changing the smallest nondescript parameter beyond its normal bounds. Because supply chain models (such as those describing a typical manufacturing company) can be complex, there are sometimes multiple parameters that lead to instability and these are not always easily identified. When superimposing unpredictable human behaviour and recognising that the even best of mathematical models are merely an approximation of reality, it should come as no surprise that many manufacturing supply chain models fall short.
Supply chain experts argue that the bulk of the payback on a supply chain model is achieved in the last few percent "fit" between the model and reality. In other words, a model that is perhaps 80% accurate is practically useless; one at 96% accuracy may offer some value, but a model that is 99% accurate is capable of delivering all the benefits you expect.
"Big button" approach
When faced with this problem, many companies seek to rectify the inaccuracies in the model by improving the accuracy of the model itself and feeding it better source data. There is a strong temptation to do this by integrating plant to the supply chain model through MES level integration. This is because the technology is readily available and because it is perceived to be easier to integrate computing systems to each other than to integrate humans to a computer system. By eliminating "human error", it is argued, the models will become more accurate and eventually human decision-making can be eliminated altogether. The concept is that "one big button" can be pressed and the entire supply chain will optimise itself with the aid of sophisticated mathematical models.
By eliminating "human error", it is argued, the models will become more accurate and eventually human decision-making can be eliminated altogether.
Gavin Halse, MD of ApplyIT
What is not readily understood by proponents of this approach is that the moment human decision-making is taken away and relegated to a "black box", production staff lose their sense of accountability, and lose touch with the underlying rationale of production decisions. Should the model then subsequently become inaccurate or unstable, the production staff will be disempowered to take corrective action.
Once again, as in most manufacturing system design, the answer lies in striking a balance between the supply chain model and human decision-making. An effective supply chain tool should help the planners and production personnel make decisions by showing the consequences of certain alternative actions.
Planners need to plan
Planners still need to be responsible for basic planning, but in order to be efficient they need the best tools to help them with this task. The best supply chain solutions are like the electronic systems of a modern aircraft - there to take over the mundane tasks but never to take away final accountability of the pilot to fly the plane safely.
It is revealing that even the most sophisticated and proven avionics systems are only used occasionally and in extreme situations to land an aircraft. In almost all other circumstances, the pilot will outperform the best state-of-the-art aircraft systems.
Are we then being realistic to expect our supply chain software to run our business, in an environment where there are many more unknown factors, and where the underlying stability of our supply chain is questionable? Of course not! We intuitively know that success will come from empowered people making the right decisions because they have the right information at hand. The secret is to regard our production planners as the "pilots" of our supply chain. They have an element that no computer system can ever emulate - intuition.
With that premise, ask the planners what tools they need to do their job most effectively. The answer may be a surprise - it is almost certain that few planners will favour the "black box" model that does all the thinking for them.
Share