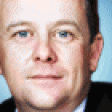
Bar code technology users no longer need to make a choice between the reliability of solid-state charge-coupled device (CCD) readers and the fast performance associated with laser scanners. A major innovation in laser scanner design and manufacturing combines reliability and performance by adapting proven, reliable micro-electromechanical systems (MEMS) technology for bar code reading.
MEMS-based laser scanners provide faster reading and better processing of poor quality or damaged bar codes than traditional lasers. They are also reliable, even in harsh environments, and because MEMS scan engines are extremely compact, scanners are lightweight, ergonomic and power-friendly.
MEMS devices combine electronic circuitry with miniaturised mechanical devices, which may include sensors, motors and pumps on a silicon substrate that can be smaller than a grain of sand. MEMS is the technology underlying antilock brakes and vehicle airbags, and is used in numerous industrial and commercial products such as inkjet printers, digital televisions, optical networking gear and medical imaging equipment. In other words, MEM`s bar code scanning represents a new application for a well-established technology used in millions of devices.
MEMS motors and other components can be smaller in diameter than a human hair. Components are assembled on silicon using integrated circuit production techniques. Further processing can be used to etch away parts of the silicon wafer or to add additional components.
Bar coding scanning basics
Like traditional laser bar code scanners, MEMS scanners use a mirror to focus and direct a laser light source to scan a bar code symbol. The symbol is decoded in the traditional manner, with a sensor measuring the amount of light reflected back. The light measurement is converted to a digital signal and the decoding algorithm is applied. However, the MEMS scanner uses a lens to collect reflected light, which optimises the laser scanning process. Traditional laser designs can`t accommodate separate lens and mirror assemblies, so the mirror does double duty to reflect and collect light.
MEMS-based laser scanners provide faster reading and better processing of poor quality or damaged bar codes than traditional lasers.
Andrew Fosbrook, MD of ProScan Systems
The mirror assembly and scanner size are the most important differences between traditional and MEMS laser scanners. Traditional scanners use a motor to oscillate the mirror to move the laser beam across the symbol. The scan speed is expressed as the number of times the beam can be swept over the symbol each second.
Motorised mirrors have proven problematic for traditional laser scanners. The mirror assemblies are soldered or wired into place, which is a consistent point of failure when scanners are dropped or bumped. To reduce the chance of damage, scanners can be given heavier casings and protective rubber coatings, but these measures add size and weight to the device and reduce ease of use.
MEMS components have considerably less mass than their counterparts in traditional laser scanners, which make MEMS devices much more resistant to damage from drops. MEMS scanners are also more resistance to wear. Motors produce friction, which loosens and wears down components. Mirrors can also get out of alignment over time, which seriously degrades performance. These dangers are mitigated or eliminated in MEMS designs.
Users who value dependability often choose CCD bar code readers because they have no moving parts. Light-emitting diodes (LEDs) illuminate the bar code symbol. The light reflected back is captured and converted into a digital signal that can be decoded. The LED, light sensor and signal processor are combined in solid-state construction that has proven to perform in challenging industrial and retail environments.
MEMS scanning
MEMS scanners deliver the reliability of CCDs to the laser category because instead of having a mirror that is moved by a motor, the mirror is etched directly on silicon and uses a unique method of frictionless oscillation that requires less power and offers increased speed as well as two-dimensional (2D) matrix scanning capability. MEMS mirrors are also much smaller than mirrors used in motor-driven scanners, making them more power efficient and easy to manipulate.
First-generation MEMS scanners compare favourably with traditional lasers for range, speed and cost. Like all linear scanners, current MEMS devices are limited in their ability to process 2D symbologies and read bar codes in any orientation. Future mirror assemblies and other design changes already on the drawing board will enable omni-directional and raster scanning and extended range. The result will be MEMS scanners that read stacked and matrix 2D symbologies, as well as introduce new omni-directional reading capabilities and perform long-range reading.
MEMS is not new technology, but provides an important new option for bar code scanning. The MEMS option should be considered when extreme reliability and responsiveness are desirable in scanning operations. Until specialty MEMS scanners are released, the technology is not an option for long-range and select 2D reading applications.
MEMS scanning is advantageous for daily operations in these environments, providing long-term reliability and total cost of ownership benefits. MEMS-based bar code scanners meet or exceed the speed and range performance users expect from common laser scanners while setting new standards for dependability and size. Ironically, the forthcoming innovations in materials, components and design that are expected to rapidly improve scanning performance may also help make MEMS scanners even smaller and more power efficient. MEMS scanners will also benefit from innovations to components and production techniques shared with larger and more established MEMS applications.
Share