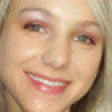
Michelle has a great idea for a new all-purpose remote control. Armed with a bit of start-up capital, a solid business plan and a killer sales pitch, she wants to give potential clients a demo model they can hold and feel for themselves. The cost to create a tool to produce Michelle's single prototype remote? An easy R50 000.
Luckily, the options don't end there. 3D printing can save innovators like Michelle thousands in planning and production costs by literally 'printing out' her design, and having it ready in a day's time.
For entrepreneurs and small companies, 3D printing can mean the difference between a deal and major disappointment. It can save them the cost, time and resources involved in conventional prototyping processes, and do some pretty nifty things besides. Like creating exact replicas of one's face, or the toy a child has just dreamed up, or spare parts for a rare machine.
3D printing, rapid prototyping and additive manufacturing are terms used for a set of technologies that describe the rendering of designs into 3D form, through an 'additive' layering process.
The term 3D printer is often use to refer to the powder-based machines made famous by companies like Z Corp, but encompasses various techniques differing in cost, quality and raw materials. This includes everything from basic, self-assembled RepRap machines, available for around R12 000 locally, to the high-end 'Objet' machines that go for a few million rand and print in multiple materials and colours.
Kenneth van Rensburg, co-founder of Protoform Rapid Prototyping & 3D Printing, says the nature of 3D printing allows for the creation of very intricate pieces that may be impossible to produce with other processes.
Most 3D printers work by using a 'build' material and support material, largely because they print layer upon layer, and so need a substance to build on. Johan Bester, managing member of 3RD Dimension Prototyping, says it's similar to constructing something like a garage, where scaffolding and planks are used as a support structure for the roof, and taken away after the building is complete.
“Say you were making a cube with no bottom; the top of the cube needs to be built on some kind of substructure, and once finished you can take it out and you're left with a cube with one side missing.”
One day you might be able to print the whole bonnet of a car in one go.
Johan Bester, 3RD Dimension Prototyping
There are various types of 3D printing, but all function by gradually building up material in extremely thin layers, often only hundredths of a millimetre thick. A designer or engineer will create the object in 3D using computer-aided design (CAD) software and the CAD file is imported into the system. The software then slices the 3D drawing into very thin cross-sections and sends the data to the 3D printer, which 'prints' these cross-sections one at a time, creating the final shape.
A fairly common technique uses a process similar to standard inkjet printing, with powder and a binder being fused to create a solid but brittle material. The cartridge prints the cross-sections by spreading a thin layer of powder and depositing the binder, bonding the two together. As the platform drops down, a new layer of powder and binder is printed, with each layer fusing to the next.
The process is repeated until the item is finished, and can take several hours. The excess powder is carefully brushed away after which the item is dipped in a tank of superglue formula, which infuses the model, strengthening and binding it together.
Protoform uses this kind of printing to create everything from tiny decorative chess pieces to fully-formed chairs, zany bar counters for TV sets and even artworks. One advantage of this technique is that because it uses inkjet technology, objects can be printed in full colour.
Outer limits
The possibilities of 3D printers depend only on one's imagination, and the physical limitations of the machine. Van Rensburg says Protoform makes anything from miniature yachts to scale models of stadiums, malls and houses.
“If you're at a boat show, for example, and the final vessel hasn't been manufactured yet, you can print a prototype to show people exactly what it will look like.”
The difference is, instead of having to painstakingly put together hundreds of small parts, the entire shape can be printed in one go.
Another benefit is the ability to make specialised parts on demand, which can prove extremely useful when far away from a supplier, says Bester. A local facility can call up the appropriate spare part online, download the design and simply print it out.
This can be particularly helpful when somewhere really remote, like in orbit. “Nasa has a 3D printer that travels on the [international] space station in case something breaks because they can't take along tonnes of spare parts,” notes Bester.
For stronger, more durable objects or parts, a fused deposition modelling (FDM) machine, like the one Bester has, might be better suited.
In this case, the material used is molten heavy-duty plastic, which gets fed through a syringe and precisely laid down, hardening immediately. “It's similar to the plastic cord used in garden edge-trimmers, like thick fish line, with one reel of ABS plastic and one reel of support material,” says Bester. The plastic is liquefied and deposited following a tool path defined by the CAD file, with the support structure laid down in a honeycomb pattern and removed afterwards, he adds.
Then there are the expensive but highly precise 'Objet' 3D printers, of which Joe Du Buy, founder of rapid prototyping company Liquid Edge, has one of only seven in the country. At around half a million rand, his 'Eden' printer didn't come cheap, and the raw material is also heavy on the pocket.
“For an extra million, I could have gotten the Objet Connex - the granddaddy of 3D printers,” says Du Buy, referring to the super-accurate machine employed by multinational companies like Gillette to print out millions of items in multiple materials and colours.
“It allows you to print multi-textured objects in one go, such as the rubberised button and hard base of a gate remote, or the flexible sole of a shoe with a harder material on top.”
Essentially, you go into the doctor's room, scan your ear, and from that scan create an ear piece that fits you perfectly.
Kenneth van Rensburg, Protoform
The Objet machines use a liquid gel build material that jets lay down in layers, with a UV light 'curing' each layer as it's produced. The support material is a less dense gel, which is discarded once the item is fully printed.
The Eden prints in 0.016mm layers, which Du Buy says makes for a much smoother, polished finish. “Imagine you were building a rondavel house; if you build it using big concrete blocks, you're going to end up with a six- or eight-sided shape house, without a smooth curve. But if you use small clay bricks, you end up with a 2 000-sided shape house, so it has a smooth, round curve.”
If printing a coffee cup, for example, the machine lays down the ring, support material and cures the layer all at once, in microns of a second, repeating this thousands of times until the object is finished.
“It's very expensive, but helpful if you want something like a hairdryer with two parts. You can print both the hard handle, with text if you want, and the rubber insert at once.”
While the commercial benefits are clear, Van Rensburg stresses that the capabilities of 3D printing extend far beyond engineering and product prototypes. One project Protoform was involved in saw it print the busts of three local innovators, along with objects conceptualising their ideas, for the 2009 Design Indaba conference. It pushed the boundaries of creative design and production, and according to Van Rensburg, demonstrated a new movement in art-cum-engineering.
Demos on demand
For years, producing anything from a piece of plumbing to an action figure relied on a process called plastic injection moulding, which was also often the only option for creating prototypes. 3D printing has become a popular alternative to this method, which requires the costly and time-consuming creation of a tool for the mould. To make a tool for producing DStv decoders, for example, could cost almost R300 000, says Bester.
Typically, a 'subtractive' technique was used which involved cutting away at a solid block of material until the desired shape was achieved. Replacing this with additive technology to create a tool path cuts production time, and uses fewer raw materials.
Also, notes Du Buy, if a company spends huge amounts to create a model and then realises it has forgotten something, or there's a flaw in the design, it results in huge losses. “With 3D printing you can literally have the item the next day, often for under a thousand rand.”
Bester says he's constantly being approached with ideas for new plastic injection moulds, which range from the ordinary to the outrageous. “Cape Town Film Studios brought in a standard pistol and wanted to add certain features to make it look spacey for their filming of a new Judge Dredd movie.”
Often customers require a once-off, high-precision item. “Say you have an idea for a tamper-proof lock you want to go on a 40-foot container, so it can only be unlocked with a special tool. You can produce a design prototype on the 3D printer, make changes if necessary, and keep printing prototypes until you're satisfied. The tool for the final item could still cost you R500 000, but at least you haven't made any costly mistakes.”
Industrial uses aside, 3D printing also proves handy when more personal one-of-a-kind requests come along. Bester recalls printing 25 special bottles as thank you gifts for a wedding for a few thousand rand. “The technology is too expensive for manufacturing but much less expensive than getting an engineering shop to make the bottle for you,” says Bester.
Low-volume product design is an area Van Rensburg has seen a lot of interest in, as it's a helpful solution for limited product runs or when the item isn't pre-ordered. “If a freelancer or SME needs 200 custom USB sticks as a corporate gift, for example, then we would print a master mould in silicon, from which they could create the items. It's more labour-intensive but it's also more cost-effective, coming in at say R12 000 instead of several hundred thousand rand.”
I spend about 10 calls a day educating people about what 3D printing is.
Joe du Buy, Liquid Edge
Du Buy, who has a background in traditional manufacturing, says his biggest challenge is that so few people know about the benefits of rapid prototyping. “I wish I could go back to all those guys that walked out of my office years ago after hearing what a prototype would cost and say 'hang on, there's a cheaper way'.
“I spend about 10 calls a day educating people about what 3D printing is.”
Du Buy has gotten some interesting requests in his time, from energy-efficient heaters to sex toys, and admits he doesn't always know what the objects are for. “Every model, every product, every call is brand new, so every day is exciting. You name it, you can print it - that's the beauty of this technology.”
While 3D printing is finding favour with both individuals and companies for prototypes, using it for the actual manufacturing of products on a large scale is still being investigated. One of Bester's custom wedding bottles on the FDM machine takes 40 minutes; a DStv decoder: six hours; and an 8cm by 8cm coffee cup on Du Buy's Eden: 20 hours. Not exactly a recipe for mass production.
For now, it seems the personalised aspect of 3D printing is the feature inspiring designs around the world, with fashion items like custom-printed shoes and even a printable bikini making headlines. While Van Rensburg says this trend hasn't caught on locally, the country is seeing the emergence of a far more significant development than custom-made footwear - that of printed human body parts.
Out-of-body experience
“We've recently been doing work on medical 3D printing,” says Van Rensburg, saying it offers a highly effective way to measure and fit implants and prosthetics. “Essentially, you go into the doctor's room, scan your ear, and from that scan create an ear piece that fits you perfectly.”
Another application is pre-operation planning in maxillofacial surgery, which allows doctors to plan the entire operation on a patient-identical replica printed by the machine. “You take a CT scan of someone's tumour or gunshot wound and turn the scanned image into a 3D file, which can be replicated into an exact model of their jawbone or skull,” explains Van Rensburg.
“3D printing used in conjunction with other technology becomes much more powerful.”
If someone is in a car accident and sustains a major facial injury, a skull can be created from the 3D CAD file and used to craft inserts to fill up a cheekbone or eye socket, he adds. These inserts can then be printed in titanium or stainless steel, so before the doctor even begins operating, she knows exactly where to place the screws, pins or plates, and they'll fit perfectly.
Carol Spence, a qualified oral hygienist and trained digital radiologist, helps doctors to plan surgeries virtually through software manipulation. Spence takes the CT scan and imports the image into a 3D software program, creating a 3D image of the data. She then sits with the surgeon and plans the operation on the computer.
“If a patient has a massive tumour on their lower jaw, for example, you can remove it using the software and mirror-image the other side of their jaw to make a normal-looking mandible,” she explains. Using the 3D printed model of the patient's jawbone, a medical devices provider can create thin plates that bend around the model, and when the surgeon has removed the tumour, he can fit the plates without having to do any adjustments.
Taken one step further, 3D printers could eventually be used to create objects from human tissue. This process, called bioprinting, would allow doctors to 'build' organs using tissue grown from the patient's own cells, eliminating the risk of rejection involved in transplants.
Philip Hugo, a researcher at the University of Stellenbosch's Rapid Product Development Laboratory, says doctors are very excited about the potential of 3D printing capabilities. “There is a big future in the medical industry for these technologies.”
What dreams may come
The idea of having a 3D printer in every home conjures up some enticing scenarios: never again do siblings have to battle for ownership of the remote - print as many as you like. Lost a key or earring? Create another in minutes. Faulty kitchen appliances can be replaced by simply pressing 'print'. But Gartner research director Pete Basiliere says this is still some way off.
In a recent analysis of the technology, he explains that while 3D printing is advancing, it hasn't yet found an application or business opportunity beyond the use by product designers, engineers and architects that truly fulfils its potential.
“An important tipping point was reached in 2010 when HP became the first 2D printer manufacturer to offer its own 3D printers,” says Basiliere. He argues that as the first traditional printer manufacturer to enter this market, HP gives low-cost 3D printers credibility, and could potentially set standards that others will have to follow.
Created in collaboration with 3D printer developer Stratasys, known for its FDM models, the Designjet 3D printer uses ivory-coloured ABS material, and is available for around $13 000. The colour version can produce single-colour parts from a selection of eight colours.
Used in combination with 3D scanners, entry-level printers could become accessible to many more people, as it cuts out the need to create a CAD design oneself. The scanners relay the dimensions of a physical object to the system, which uses the information to create a design which can then be loaded onto the 3D printer.
Talk show host Jay Leno turned to 3D scanning when he needed to patch up one of his vintage cars, which at more than 100 years old, didn't have any spare parts floating around. Leno said rather than pay a machinist to copy and build the part, he decided to redesign the original using a 3D scanner and printer. The scanner allowed him to create an exact digital copy of the real, worn-out part, and then print it out in plastic to make a mould.
Bester says that as the technology becomes more affordable, more people are “jumping on the bandwagon”. “If I can buy a machine with my finances, a lot of other people out there can do the same. Rapid prototyping as a whole is going far - it's the future.”
However, Van Rensburg notes that the widespread use of 3D printers could introduce some significant intellectual property issues, especially in SA. “Because it's such a new and emerging technology, local lawyers and patent attorneys are not prepared for what might happen if 3D printing goes mainstream.”
According to Web and digital media lawyer Paul Jacobson, 3D printers increase the range of things people could copy and the types of intellectual property they could infringe.
“Like the Internet allowed for the infringement of copyright on a larger scale, so 3D printing makes it possible to produce products that infringe on designs, patents and trademarks as well.”
He says whether 3D printing will be considered infringement will depend on its use - personal versus commercial purposes, for example.
“It comes down to the specific circumstances you're dealing with. But the technology does open the door and if you throw 3D scanners into the mix, you face a situation similar to the one that arose when photocopiers came out, with the sudden ability to photocopy books.
“The potential for abuse is there and whether it happens depends on the availability of devices to the average person and what they do with their creations,” says Jacobson.
Du Buy adds that the printer is also only as good as the data plugged into it. “A 3D printer is very clever but very stupid. Like a TV or PC monitor, it can do nothing unless you give it a 3D CAD design.”
There's also the requirement for uninterrupted power supply, because if the printer is suddenly interrupted, one has to throw the unfinished object away and start again. A pretty expensive exercise, says Bester, who has a UPS for this very reason.
“The technology is still a little limited,” he adds. “It's like when you're baking a pancake - if you only add the eggs 70% of the way through, it's not going to work. In the same way, when the machine is building the layers, there's a certain time span during which it can lay down the next layer, otherwise it won't set.
“If the techies can go further with the materials, 3D printing can go further and rapid prototyping can go further. One day you might be able to print the whole bonnet of a car in one go.”
Despite the current limitations, Bester says 3D printing essentially allows one to turn imagination into reality.
“In a race called 'Quads for Quads' we spent four days on quad bikes in the bush to raise money for quadriplegics. One of the guys driving with us, Dr Cival Mills, is a former doctor who can only move his left arm and hand after surgery for a car accident left him with locked-in syndrome.
“I wanted to give him something to honour the fact that he rode with us for four days in a specially-modified quad bike, so I drew up a wheelchair with suspension and quad bike wheels, printed it, and mounted it on a trophy block for him.
“As long as it's within the limits of the machine, you can pretty much print anything.”
Share