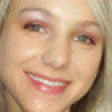
If you've ever had to move house, spring clean or simply sort your drawers, you'll be familiar with the vast pile of “stuff” that accumulates seemingly of its own accord. Bits 'n pieces of odds and ends that gather to form a messy junkyard; the cast-offs of a consumer society.
Waste, which makes up around 40 million tonnes a year in SA alone, is something of a foreign concept in the natural world. Here nothing is redundant - blossoms fall to the ground and decompose to form food for other plants, and seeds are encased in fleshy fruit or hardy shells, eventually becoming the source of new organisms.
It isn't impossible, costly or backward to make electronics from recyclable materials.
Lezette Engelbrecht, online features editor, ITWeb
Nature manages to produce, grow, package and dispose of its products without a single element of waste. This ongoing cycle of life begets life creates a system in which everything retains value.
Human production, however, is a little less efficient. Scores of shiny, feature-packed electronics made from toxic materials are packaged in layers of plastic and enjoy a short life before being relegated to the garage. They finally join other digital leftovers in already overflowing landfills as we plough through the next stream of gadgets.
Buying new things wouldn't be so problematic if products were easy to reuse. But as Annie Leonard notes in the 'Story of electronics', most devices are “designed for the dump”.
In the race for bigger profits, companies constantly release new gadgets or new versions, along with a matching set of accessories, which last a few months before being replaced. And given the incredible rate of digital newcomers, the buy-dump cycle is picking up speed.
The traditional response is... reuse as much as you can. But this places the emphasis on treating the problem instead of negating the need for a solution altogether. As Michael Braungart, co-author of the book 'Cradle-to-cradle, reinventing the way we make things', notes, the point is to do good, not less bad.
This requires going back to the drawing board and rethinking the entire chain of design, production and disposal. Designing sustainable products made with safe materials, which are constantly reused, erases the need for waste management, because waste manages itself.
And it's beginning to happen. Innovation can be seen both in the efforts of major consumer electronics companies and smaller teams of forward-thinking developers.
A group of students from Stanford and Finland's Aalto University, for example, has used the concept of modularity to create a laptop which the user can disassemble in less than three minutes, without so much as a screwdriver. Its circuit board, screen and keyboard can all be slotted in and out, and once it's taken apart, the laptop's individual parts can be recycled.
The prototype, called Bloom, even has a postage-paid envelope behind its display to pop the parts into and send off to a recycling facility. Bloom's modular construction also means if a single part breaks, you replace just that item, not the whole machine.
One has to see the laptop to really appreciate its design, but the idea is that making it easy to disassemble will mean consumers are more likely to recycle its components. It's much simpler to figure out which bit goes into which bin. While the Bloom laptop is a concept model and won't be released to market, it serves as a nifty example of what can be done with a bit of ingenuity
Dublin-based MicroPro released a similar computer in May last year, the iameco - a 100% biodegradable model that contains no hazardous materials and also features modular design, making the individual parts easily recyclable and reusable.
Sustainable design doesn't translate into a dinky, second-rate performer either. The iameco can run various applications, all the way to 3D gaming, and is said to last between seven and 10 years.
Other companies have spruced up the materials used in manufacturing. Fujitsu, for example, has substituted renewable materials for plastic in its key board and mouse components. The latter is biodegradable and completely recyclable.
As for the keyboard, 45% of its plastic components are replaced with materials from renewable sources. There's still a way to go, but it does helps eliminate the use of oil-based substances like hard plastic and PVC from the manufacturing process.
Fujitsu estimates that by making the switch to renewable materials for this product, it saves approximately 60 000kg of plastic per year.
These efforts and innovations are a sign that shift can happen. That it isn't impossible, costly or backward to make electronics from recyclable materials, and cut the concept of 'waste' out of the production cycle altogether.
But then, rewiring generations of industrial design, corporate thinking, and consumption patterns was never going to be easy. As with other environmental initiatives, cradle-to-cradle design will have to emerge as the easiest, cheapest and most functional option for it to acquire mainstream adoption. Positioning this shift in terms of efficiency, rather than morality, is likely to win over more supporters.
As Braungart puts it: “I'd frame it as 'let's not be stupid' rather than 'let's be ethical'. Look at the 'quality' of everything we do, design things the right way - that is more likely to lead to solutions.”
Share