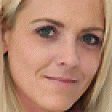
A new faster, larger additive layer manufacturing system (ALM - commonly dubbed a “3D printer”) being developed in SA could change the way components for the aerospace industry are made. It could also open up new design innovations and save the industry significant amounts of capital.
In what is claimed is a world first for manufacturing technology, SA's Council for Scientific and Industrial Research (CSIR), and aeronautical engineering and manufacturing company Aerosud are developing technology that improves on today's commercial manufacturing systems. This allows for the creation of much bigger components.
The project, which has been funded by the Department of Science and Technology (DST) to the tune of R37 million over the past 18 months, is expected to come to fruition mid next year, when the technology firms plan to switch the system on.
Faster and bigger
According to Hardus Greyling, operations manager of the National Laser Centre at CSIR, the machine, the prototype of which is being built at the council's National Laser Centre, is an additive manufacturing system as opposed to a 3D printer. He says it makes use of a laser beam that is rapidly scanned across a bed containing metal powder - in this case titanium.
While the several other commercial systems on the market currently operate on the same principle, Greyling says this system - an “unprecedented innovation” - is much faster and larger.
“The CSIR and Aerosud have invented a novel approach that will allow the building of much larger components, much faster than conventional ALM systems. We focus on using titanium powders, with the ultimate goal of building components for the aerospace industry.”
While the project is aimed primarily at producing parts for the aerospace industry, Greyling says the technology will also be applicable to other manufacturing industries, such as the manufacture of medical implants.
Major benefits
Greyling says the advantages of the ALM system include the ability to build components that are very complex, and not possible with current manufacturing technology.
“We don't start with a large solid piece of material and then machine away what we don't want, creating a lot of wastage. Titanium is an expensive material and in this technology, we build the component from powdered material, implying huge savings in raw material. Unused powder can be re-used for other components.”
The machine will have significant implications for original equipment manufacturers and the aerospace industry at large, says Greyling. “It will introduce a new method of manufacturing large components for the industry. The benefit will be in that there will be cost savings from a material point of view, and the technology will also open up possibilities for new design innovations.”
In addition to this, he says, the fact that this is a South African development, will position the local aerospace industry in a strong competitive position for the manufacturing of titanium components for aerospace applications, and will most likely increase their global market share.
“The technology is also an important link in the value chain of the government's titanium industry establishment initiative; in that it will provide a capability as one more manufacturing technology to beneficiate locally produced titanium powders, which is at present being developed within the titanium industry development initiative of the DST.”
Share